Tangential Flow Filtration: A Complete Guide for Bioprocessing Professionals
Tangential flow filtration plays a critical role in the research, formulation and production of life-saving biopharmaceuticals within downstream bioprocessing. This comprehensive guide to tangential flow filtration will explore applications, benefits, and criteria for choosing the right tangential flow filtration system.
What is Tangential Flow Filtration (TFF)?
Tangential Flow Filtration (TFF) is a method of separating, purifying, and concentrating therapeutic biomolecules. This method is applied by the feed solution flowing parallel (or tangentially) across the membrane surface instead of directly through it. This tangential flow generates a sweeping or lifting force at the membrane surface that picks the retained material up and allows it to flow out of the retentate end of the filter device rather than leaving it deposited as a fouling layer. This effective method of filtration allows large and small volumes to be processed with less membrane surface area and lower risk of filter fouling than normal flow filtration (or dead-end filtration). It enables recovery of both the retentate and permeate as well as the possibility of rinsing and reusing membranes.
Tangential Flow Filtration Applications
Used for research, product development, and manufacturing, TFF is a critical filtration technique used throughout the bioprocessing workflow. The following list provides a summary of common TFF applications and their definitions.
Cell Harvesting
The separation and recovery of cells from fermentation.
Lysate Clarification
The separation and recovery of target molecules from cell debris (membrane fragments) and intact cells following cell lysis.
Product Fractionation
Protein separation based on molecule size.
Concentration
The concentration of retained proteins by removing unwanted solvents and small molecules.
Diafiltration
The exchange of buffer solution to final buffer formulation for additional processing.
The applications cited above can be used, but not limited to, the processing of the following modalities:
|
|
|
Types of membranes used in Tangential Flow Filtration
Membranes are available in a wide range of materials and configurations for a variety of applications. The two common types of membranes (or filters) used in TFF are Flat Sheet Cassettes and Hollow Fiber Modules.
Flat Sheet Cassettes
Constructed by several layers of membrane stacked on top of one another with a woven mesh screen in-between the layers, flat sheet cassettes are ideal for processes that demand higher flux. As product flows through each of the mesh layers, the feed is forced into a turbulent flow. The advantage of turbulent flow is that it enhances the sweeping of the membrane surface and prevents material from building up and fouling the filter. Non-enveloped viruses such as AAV (Adeno-associated virus) are less sensitive to shear forces and benefit from the higher flux of a flat sheet cassette within TFF.
Hollow Fiber Modules
Made up of a simpler flow geometry than the flat sheet cassette. Hollow fiber modules are cylindrical structures that house a bundle of tubular self-supporting fibers. With this format, the feed travels through the hollow fiber lumen in a very laminar flow, resulting in lower shear and gentler processing. This makes hollow fiber modules an ideal option for enveloped viruses like lentivirus that are more shear sensitive.
Ready to shop for membranes?
Repligen has one of the widest selections of membrane formats, sizes, and chemistries in the market with TangenX® Flat Sheet Cassettes and Spectrum® Hollow Fiber Modules.
Optimizing Performance for Tangential Flow Filtration
The efficiency of TFF performance is a balancing act of finding the correct membrane chemistry and format, and the right combination of transmembrane pressure (TMP) and cross flow flux (CFF) rates. How accurately the pressure and flow rates can be measured and controlled has a direct impact on the performance and efficiency of your TFF process. If the TMP is too high then the gel layer formed on the membrane becomes too dense, severely restricting the flow to the permeate. If CFF is too high, more molecules will pass through the retentate reducing permeate flow, resulting in extended processing times that could jeopardize the end product. Additionally, an improper pairing of the pump’s flow rates with the tubing inner diameter (ID) and strength can cause cavitation or fluid velocities which can damage product. For these reasons and more, selecting the right TFF system and membrane are key to optimizing microfiltration, ultrafiltration, and diafiltration (UF/DF) performance.
Tangential Flow Filtration Systems Versus Manual TFF
The typical manual or semi-automated TFF set-up consists of pumps, scales, pressure gauges, manual valves, sensors, tubing, and vessels. Usually sourced across various suppliers, manual TFF also requires the integration and, perhaps, validation of these components prior to engaging in any unit operations.
Beyond set-up, the biggest challenge with manual TFF processing is the burden it places on the operator. Continuously monitoring to maintain the set-up, ensure consistency across all process parameters, intervene when needed, and manually document all data points puts a strain on the user. Moreover, all of these manual steps present opportunities for operational errors and compromised data integrity, which can result in extended process development, batch inconsistencies, or scale-up challenges.
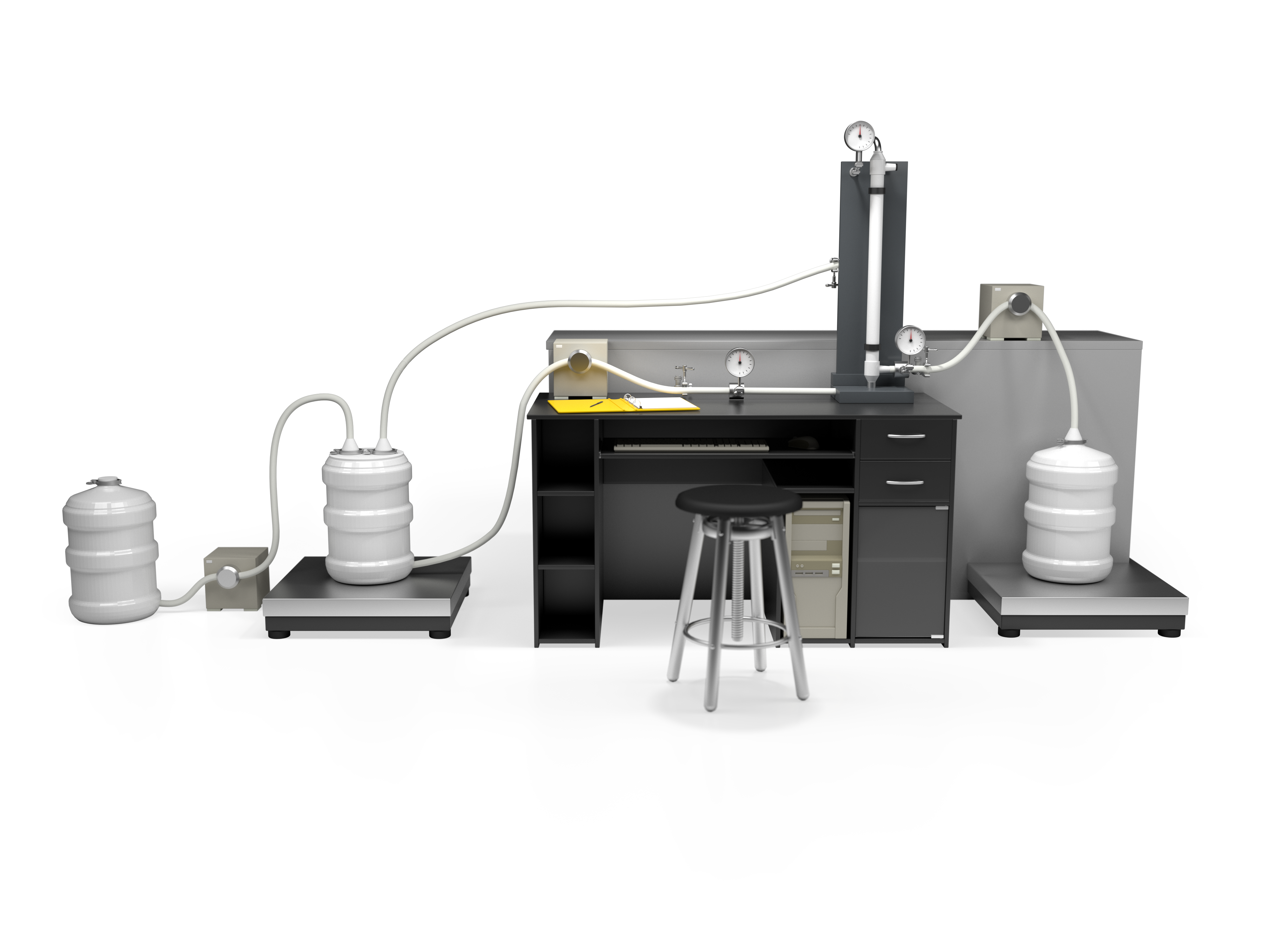
Automated TFF System |
Manual TFF Processing |
|
---|---|---|
Automated processing | ✔ | x |
Monitor and analyze data using system software | ✔ | x |
Process consistency with programmable recipes | ✔ | x |
Notifications, alarms, and set points to maintain safe operating conditions | ✔ | x |
For bioprocessing companies with the intent to manufacture, these inefficiencies drive increased operational expenses and weakened profit margins. For these reasons and more, the industry as a whole continues embracing and integrating automated TFF systems as part of their process.
Benefits of Using Tangential Flow Filtration Systems
Tangential Flow Filtration systems alleviate many of the difficulties inherent in manual TFF processing. TFF systems generally arrive tested and ready to use with all of the pumps, sensors, valves, and other components necessary for standard operations. The software used to control a TFF system allows users to not only automate process control, but also securely document, transfer, and review process data. This is critical for ensuring compliance and maintaining data integrity.
Depending on the TFF system’s software, prompts and alerts can be used to keep operators informed on the status of their process or notify them of changes needed. A more sophisticated TFF system may include features like recipe-driven control to automate entire unit operations, trending software to help visualize and plot process steps, or networking capabilities to remotely monitor and control the operation. For example, Repligen’s KlariFi™ software, comes standard with all of these features, including a dedicated recipe template library built and curated by TFF experts. Depending on the system supplier, customization options and additional connectivity features may be available upon request. These capabilities empower operators by minimizing the risk of error associated with manual tasks and increasing operational efficiency thereby reducing costs.
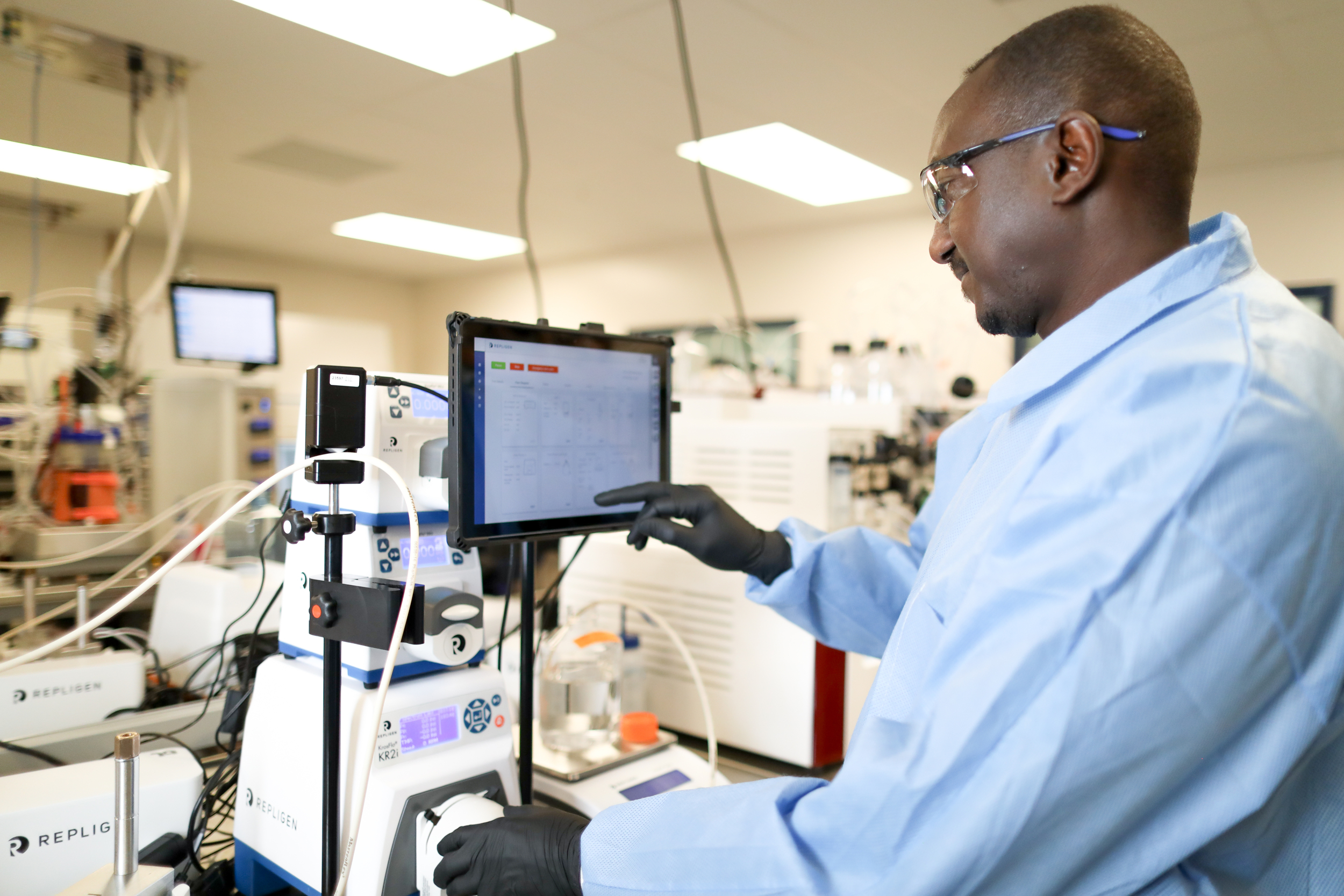
Choosing the Right Tangential Flow Filtration System
Selecting the ideal TFF system is not a one-size-fits-all approach. Factors related to process requirements, automation capabilities, ease-of-use, budget and compliance all have an impact on the selection process. TFF system requirements for research students in an academic laboratory will strongly vary from the needs of operators producing therapeutics. So, understanding what the goals and user requirements are becomes key to the selection process.
Beyond any present research or formulation development, consideration is also needed for future planning. In many cases scalability, for example, is a critical factor for selecting a TFF system because it will directly impact production capabilities. An inability to increase production volume within allotted deadlines while maintaining quality standards creates bottlenecks that put projects and even pharmaceutical companies at risk. Therefore, choosing the right TFF system has to account for present and future bioprocessing needs.
Ready to shop for TFF systems?
From process development to cGMP manufacturing and every step in between, KrosFlo® TFF systems make up one of the most innovative and comprehensive TFF system portfolios in the industry. Find your next TFF system now or connect with an expert to map out your ideal solution today.
Innovations in Tangential Flow Filtration Technologies
TFF technologies are constantly evolving to meet the growing needs of new modalities while exploring process improvements for familiar biologics like monoclonal antibodies (mAbs). Coupled with the rising costs of goods and labor, the demand for operational efficiency solutions has given rise to the development of innovative technologies to make TFF processing more accurate and repeatable.
Flat sheet cassette technology has become a significant innovation in membrane filtration, offering notable benefits such as higher permeate flow rates, increased membrane areas, and compact, reusable, and easily expandable formats. However, these advantages come with operational challenges that can hinder efficiency.
One key issue is the manual, labor-intensive process of assembling flat sheet cassettes. This involves correctly stacking cassettes, gaskets, and filter plate inserts into a holder, followed by the meticulous task of evenly torquing the holder bolts throughout the filtration run. This process is not only tedious but also prone to errors that can lead to leaks. Such leaks can cause product loss, contamination, or even exposure to hazardous materials—posing risks to both the product and personnel.
To address these challenges, innovative solutions have been developed, including:
- Hydraulic Auto-Torque Cassette Holders: Simplify and automate the torquing process for consistent and reliable performance
- Encapsulated Pre-Stacked Cassette Bundles: Eliminate manual assembly by providing pre-assembled units ready for use.
- Self-Contained Flat Sheet Devices: Remove the need for holders, clamping, or torquing, offering a fully integrated solution that eliminates the risk of product loss
These advancements enhance production efficiency while mitigating risks, making them essential for supporting the growing demands of new modality production. By adopting these technologies, manufacturers can achieve greater reliability, safety, and process optimization.
Advancements in process analytics technologies (PAT) are also opening doors to new methods of automation and control within TFF. The last couple of decades have brought us in-line conductivity and pH sensors. These have reduced the amount of manual sampling and analysis steps required during production. They have also contributed to decreases in quality control approval times, expediting TFF operations.
While recent innovations have also embraced in-line UV sensing technology, it is important to recognize its limitations. These sensors, including single and dual wavelength options, enhance analytical capabilities and support precise breakthrough detection. However, they are susceptible to oversaturation and may not be viable as primary analytical solutions in GMP manufacturing environments. This may require the adoption of supplementary technologies that comply with regulatory standards.
A pivotal development that addresses these challenges is the integration of in-line variable pathlength spectrophotometers. This technology delivers real-time concentration measurements directly within the TFF process, optimizing the use of UV-visible spectroscopy data. When integrated with an automated TFF system, this allows for immediate adjustments to the ultrafiltration/diafiltration (UF/DF) processes based on live analytical feedback, significantly improving cycle times and reducing process variability. Such real-time data utilization not only enhances operational efficiency but also ensures consistent product quality by enabling precise control over filtration parameters.
Related Products
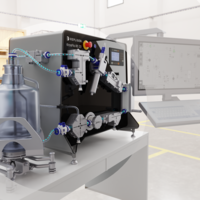
KrosFlo® Tangential Flow Filtration systems
KrosFlo® tangential flow filtration (TFF) systems by Repligen provide high-performance ultrafiltration/diafiltration (UF/DF) solutions across research, process development and GMP manufacturing. Engineered to streamline downstream processes, KrosFlo® TFF systems feature advanced automation capabilities, support most filter and membrane options, and can be integrated with advanced process analytics technologies.
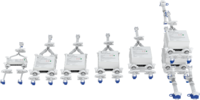
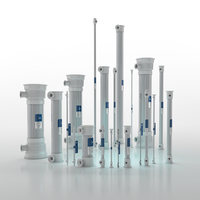
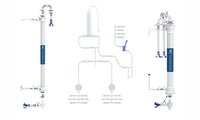
ProConnex® Flow Paths
Expertly designed plug-and-play flow path
ProConnex® Flow Paths for TFF and Chromatography processes are single-use and engineered for optimum performance, reproducibility and time savings. System specific flow paths provide speed and reliability. Configured flow paths prioritize process requirements and sterility.
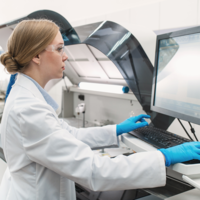
Real-time Process Management Solutions
Our Real-time Process Management (RPM™) Systems establish a new benchmark for real-time process control in downstream bioprocessing by integrating of the CTech™ FlowVPX® in-line UV-Vis spectrophotometer into the KrosFlo® TFF Systems. This innovative solution empowers users to achieve unparalleled control and optimization of UF/DF processes, driving efficiency, quality, and innovation in biomanufacturing.